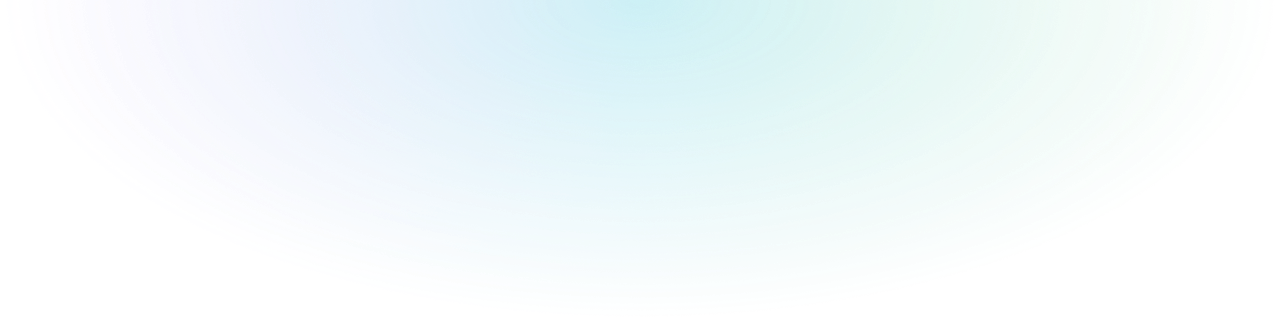
Ensure general maintenance and housekeeping standards are met
Version 1 - Last updated 23rd July 2025
A supplier should implement the following activities in the facility.
Maintenance and housekeeping
- Identify and record machines requiring maintenance.
- Schedule and track maintenance activities.
- Regularly inspect and label all chemical containers.
- Check for and remove expired chemicals from use.
- Verify the functionality of all first-aid boxes and eye showers.
- Replace or repair non-functional equipment immediately.
Housekeeping SOP
A supplier should prepare and maintain a housekeeping SOP that includes:
- Identifying and documenting machinery, components and equipment not performing optimally.
- Maintaining records as per standard operating procedures. (Refer to the template given below to track general maintenance and housekeeping).
- Scheduling and carrying out the replacement of machinery, components, PPE, equipment, first-aid box components, spill kits and store materials according to their expiry dates.
- Maintaining detailed records of all machinery and equipment servicing activities. Inspecting and identifying chemical containers that are in poor condition, unlabelled, or expired.
- Ensuring timely replacement or disposal of such containers.
- Implementing procedures for the safe disposal of unused or rejected chemical products.
- Conducting regular chemical clean-outs to manage and minimise hazardous waste.
- Regularly reviewing and updating the emergency response measures, including eyewash stations, body showers, exit signs, assembly points, exit pathways, fire safety equipment, and first-aid boxes.
The below template can be used for tracking general maintenance and housekeeping:
