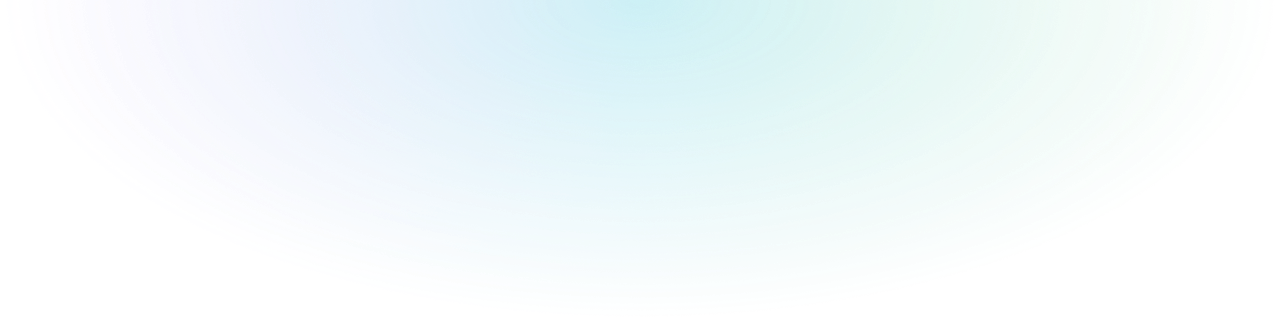
Conduct a review of the chemical management system through assessments and corrective action plans.
Version 1 - Last updated 23rd July 2025
It is vital that the chemical management system is continuously reviewed, and updated accordingly in order to ensure that any gaps/updates are identified and improvements to the system are planned.
Action Plan
The Chemical Management Strategy Action Plan should be reviewed for the scope, goals, timelines, resources and methodologies.
Additionally, continuous improvement actions should be implemented for:
- Safe chemical storage and handling systems.
- Waste management and reduction.
- Documentation and records control, incident management, and general maintenance and housekeeping.
Review Process
The review should be done through audits that consider the following:
- Who needs to be involved in the audit process?
- Who will be the chemical management system auditor(s)?
- What should the qualifications be?What is the audit frequency?
- How are the audit results and corrective actions documented?
- What possible links can be made with other audit programmes (for example quality or waste or environmental management system audit)?
- How should the audit results be communicated and reviewed by facility leadership?
Assessment Process
The audit process can be set up as per the below suggested activities flow:
- Designate competent person(s) to perform the assessment.
- Define audit scope, criteria and objectives.
- Create an audit plan (time, location, duration, audit methods and follow-up actions).
- Create an audit checklist based on goals to be checked and areas to be assessed.
- Record the audit evidence (photos, document checks, interviews, forms and samples).
- Document audit results and prepare CAP with timeline and affixing responsibilities.
- Communicate audit results to the facility management through management review meetings (MRM) to make specific decisions.
- Communicate the audit report and actions taken to relevant departments in the facility.